What are pre-engineered buildings, and how do they differ from conventional construction?
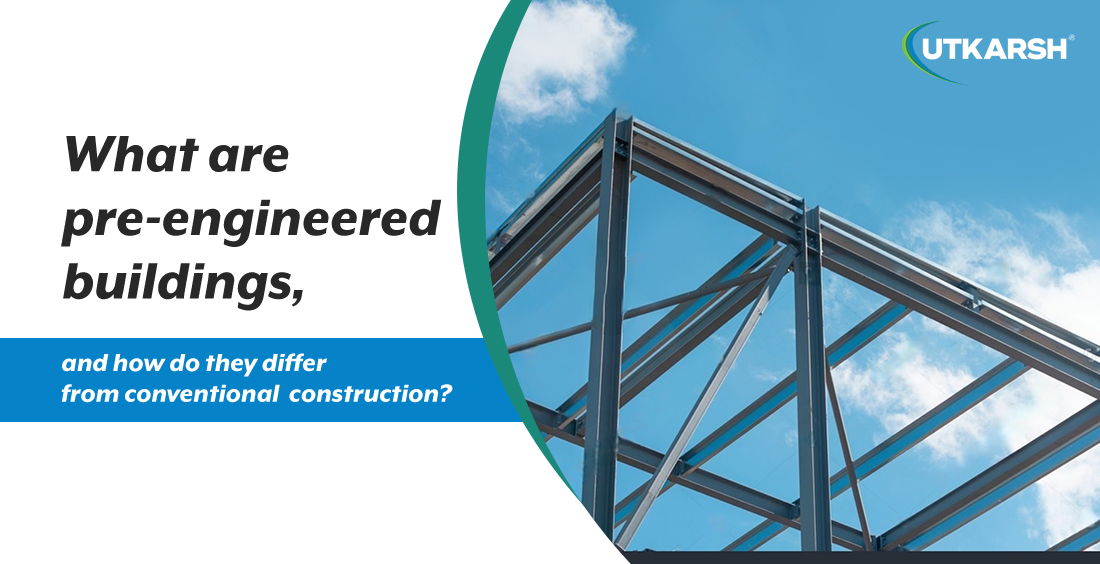
Pre-engineered buildings (PEBs) are factory-designed structures manufactured using standardised components optimised for quick on-site assembly, while conventional construction involves custom-designed elements built entirely on-site. PEBs prioritise efficiency and speed through modular engineering, whereas conventional methods rely on traditional materials and site-specific fabrication.
1. Design and engineering
PEBs use computer-aided engineering (CAE) to ensure precision. Engineers optimise every component for performance and structural integrity. Factories pre-test parts before delivery which ensures seamless assembly. Conventional construction requires custom designs for each project. Architects and engineers plan structures individually which increases planning time. Builders select and assemble materials such as steel beams, bricks, and cement on-site. The lack of pre-tested components can lead to inconsistencies in quality and durability.
2. Construction process
PEBs can reduce construction time by 20–50% through prefabrication. Factories manufacture components under controlled conditions, improving accuracy. On-site assembly follows a streamlined process which reduces delays. This controlled approach also reduces errors and improves consistency.
Conventional construction takes longer due to on-site fabrication. Workers cut, weld, and assemble materials manually which increases complexity. Manual assembly of traditional materials can lead to variations in workmanship. Factors such as mortar application, alignment, and curing processes are complex and increase cost and risk. Heavier materials require complex foundations, increasing load-bearing requirements. This process adds to project costs and completion time.
3. Materials and durability
PEBs use high-strength steel to ensure durability in extreme conditions. It resists corrosion and reduces maintenance costs over time. Advanced coatings protect the structure from rust and degradation. Engineers design PEBs to endure adverse conditions such as strong winds and seismic activity. These buildings remain stable under extreme temperature changes. Conventional buildings use a mix of materials, including bricks, cement, and rolled steel. These materials offer durability but lack the uniform strength of engineered steel.
4. Cost efficiency
PEBs reduce overall costs through automation and optimised material use. The factory-controlled environment in which PEBs are manufactured minimises waste by using precise cutting and assembly techniques. Thai ensures that materials are utilised effectively. This not only reduces material costs but also lowers labour expenses, as less on-site labour is required for assembly compared to traditional construction methods. Faster construction timelines further reduce project costs. Conventional construction incurs higher expenses due to labour, materials, and custom designs. Large-scale projects demand extensive planning and skilled workers. This increases overall costs, particularly for complex structures.
5. Flexibility and expansion
PEBs support easy expansion due to their modular design. Factories produce standard parts that fit with existing structures. This system enables quick changes without major reconstruction. Companies extend buildings without stopping daily operations. Bolted connections make modifications fast and secure. Workers add or remove sections without weakening the structure. This method simplifies extensions and avoids costly delays. As a result, businesses can increase space without changing foundations or core frameworks.
This flexibility suits industrial, commercial, and institutional buildings. Warehouses, schools, and aircraft hangars expand without major disruptions. Owners add storage, classrooms, or hangar space quickly.
Conventional buildings, on the other hand, require major changes for expansion. Brick and concrete structures need extra support and strong foundations. Modifying an existing layout often disrupts daily activities. Engineers redesign key sections to keep the structure stable. These changes increase costs and extend project timelines. Expanding traditional buildings often involves demolishing walls and shifting utilities. These factors make conventional expansion slow and expensive.
Leading PEB structure manufacturers in India ensure that all components meet strict quality standards. Factories produce parts with precision to maintain structural integrity. Engineers design each section to fit seamlessly with other components. Pre-tested materials guarantee durability and strength under extreme conditions. Manufacturers follow industry regulations to ensure safety and reliability. Advanced fabrication techniques reduce errors and improve consistency.
Looking for information on PEB manufacturing companies that focus on quality?
Utkarsh India provides high-quality PEB solutions with a strong focus on durability, efficiency, and precision. With a fabrication capacity of 1,000 MT per month, we ensure large-scale production to meet diverse project demands. All operations, including fabrication, take place in-house, allowing better control over quality and consistency. An in-house testing laboratory conducts regular quality checks on raw materials and finished products. We use high-tensile HR plates with a yield strength of 345 MPa for built-up sections. Cold-formed sections feature 120 GSM or 275 GSM pre-galvanised slit coils with the same yield strength. We source raw materials from reputed vendors like SAIL, guaranteeing the best quality for every project. To know more, contact us.