PVC Pipe Manufacturing Process Explained Step by Step
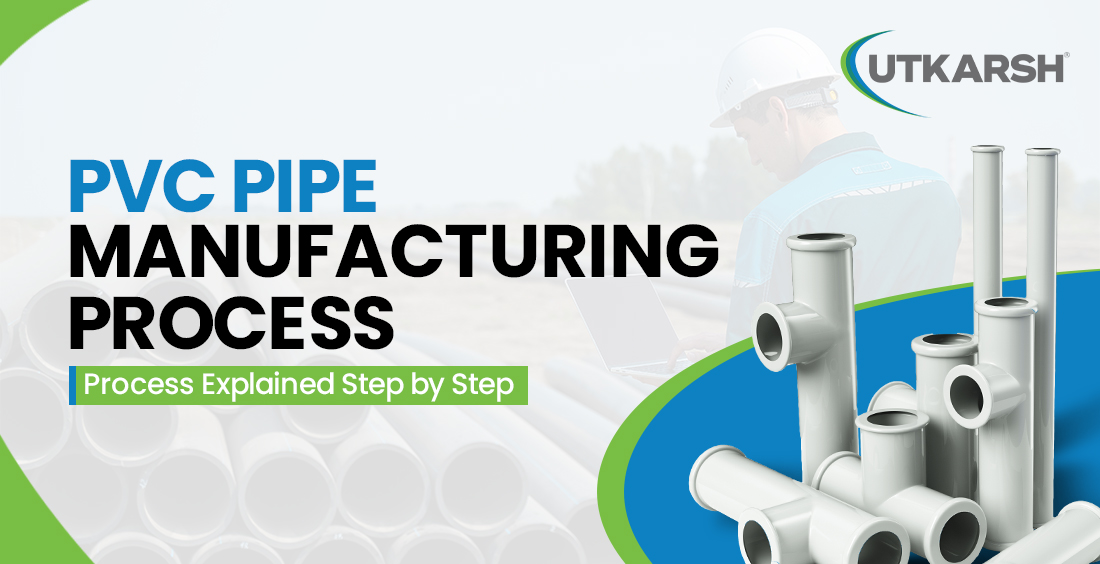
From the plumbing of your house to the irrigation of farms, light weight and corrosion resistant pipes are the favorite of manufacturers. But have you thought about the wide applications of PVC pipes? To explore the intriguing world of engineering, let’s go through the step by step PVC pipe manufacturing process, which is blended with high tech machinery, precision and skilled planning.
Raw Material Preparation
The first procedure of the PVC pipe manufacturing process is obtaining the right materials. The most crucial material is Polyvinyl Chloride resin, also known as PVC. In this case, it is not used alone. There are other components that are needed such as stabilizers and plasticizers to aid in flexibility, fillers for UV resistance and pigments to color the pipes.
To make the blend, high speed mixers combine the materials. This stage is vital because the method used to combine the materials determines how well the mixer works. If the plumbing is not adequately blended together, the quality will not meet standards.
Feeding and Heating (Extrusion)
When everything is set, the PVC compound moves onto the extrusion machine. This is the part where the action happens – no, literally; everything is heated. The compound is transferred to a hopper where a screw is rotating, and the compound is pushed through a barrel. It gets to a temperature of about 170-190°C where the material melts without burning.
Once the compound gets to the required temperature, the compound is now soft and easy to be molded. The next step is for the extruder to push this mix through a die that is exclusive, designed in a way, to give the pipes their initial shape, so the PVC pipe manufacturing can begin.
Pipe Sizing and Cooling
After extrusion, the hot pipe still isn’t strong enough to hold its shape. That’s where the sizing and cooling units come in. The freshly extruded pipe is pulled through a sizing sleeve, often inside a vacuum tank. This step helps ensure consistent diameter and wall thickness.
Right after sizing, the pipe is sent through a series of water cooling baths. Water jets rapidly lower the temperature, setting the pipe into a hard, final shape. Proper cooling is essential in the PVC pipe manufacturing process in India, especially to meet industry-standard specifications.
Cutting and Socketing
Once the pipe cools down, it’s cut to the desired length, typically 3 to 6 meters depending on the end application. After cutting, socketing may be done at one or both ends. This is the process of shaping one end of the pipe into a socket to allow easy joining with another pipe or fitting.
Socketing involves reheating one end and expanding or compressing it using socketing machines. It’s a key part of PVC pipe manufacturing that makes installation a whole lot easier.
Marking and Quality Inspection
No pipe leaves the factory floor without a thorough inspection. Each pipe is printed with key details like brand name, pipe size, pressure rating, batch number, and manufacturing date. This ensures traceability and accountability.
Then comes the testing phase. Pipes are tested for pressure, impact resistance, and dimensional accuracy. Some advanced facilities even perform burst tests or UV resistance checks. This quality control step guarantees that the pipes meet ISI or other global standards, which is a must in the PVC pipe manufacturing process in India.
Check this out: Saving money on UPVC pipes: Tips and tricks
Packaging and Dispatch
Once the pipes pass all tests, they’re ready for packing and shipment. Bundles are wrapped in protective covers to prevent UV exposure and physical damage during transport. Proper storage and handling instructions are also part of the packaging process, ensuring the pipes reach their destination in top-notch condition.
What Else You Should Know About the Process
Modern PVC pipe manufacturing often includes automation to improve consistency and reduce waste. Systems now monitor everything from pipe thickness to cooling rates in real time. Also, some manufacturers are using recycled PVC compounds in non-pressure applications to support sustainability efforts—something that’s gaining traction across the PVC pipe manufacturing process in India.
As the industry evolves, precision engineering and environmental responsibility are becoming part of the standard manufacturing playbook.
Read more: How to choose between CPVC and PVC pipes based on price and application?
Alongside these innovations, companies like Utkarsh India are making a solid mark as a trusted pipe manufacturing company. Our wide product portfolio covers uPVC, cPVC and other pipes are built for performance and reliability. Known for durable products and customer-centric innovation, we continue to meet diverse needs across sectors with consistent quality.
Conclusion
The PVC pipe manufacturing process may seem complex at first glance, but it’s a well-structured and efficient journey from raw materials to a ready-to-use product. From extrusion to inspection, every step in the PVC pipe manufacturing chain plays a crucial role in ensuring you get a product you can rely on.
With companies like us raising the bar in the PVC pipe manufacturing process in India, customers today can be confident they’re getting durable, high-performance piping solutions for all kinds of needs.