Effects of corrosion on railway mast structures
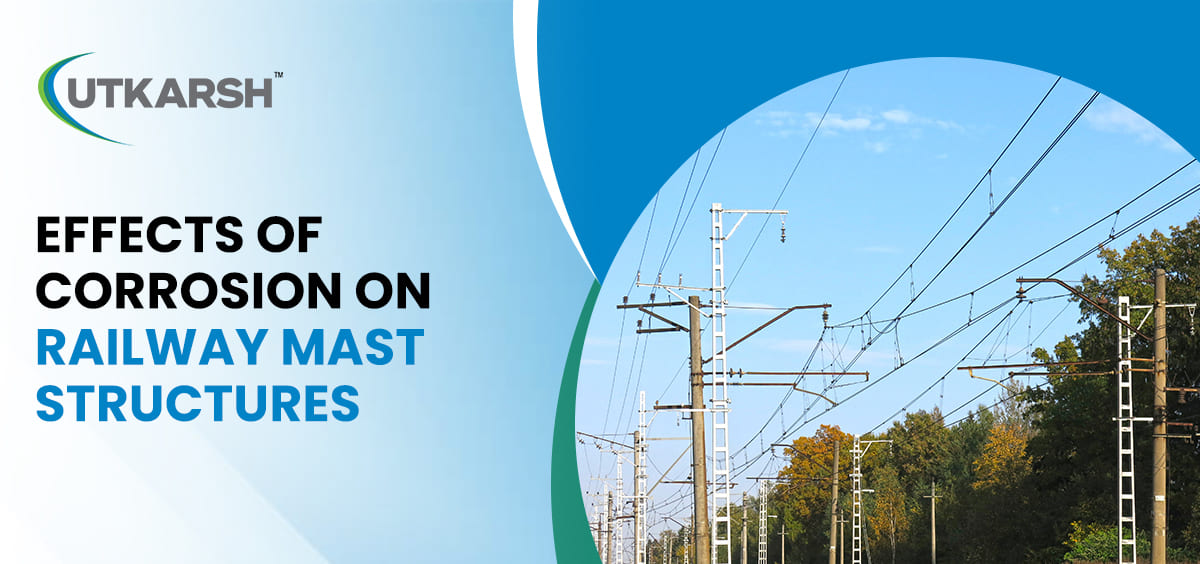
Corrosion is a natural process where materials, especially metals, deteriorate due to chemical or electrochemical reactions with their surroundings. While corrosion can take many forms, it is useful to categorise it into different types based on the specific mechanisms and conditions involved. Understanding these various types of corrosion is important for identifying the causes, preventing damage, and implementing effective corrosion control measures.
One of the common types is atmospheric corrosion which is a form of wet corrosion caused by electrolytes. In this case, moisture in the atmosphere, rainwater, and similar substances act as electrolytes, initiating corrosion on the metal surface that is exposed. Erosion corrosion is another common type. It happens when a corrosive liquid flows over a metal, leading to a faster deterioration of its surface. This type of metal wear is typically noticeable without magnification, causing visible grooves, craters, or valleys on the material's surface. Selective corrosion occurs in alloys when one of the component metals undergoes de-alloying due to the corrosive surroundings. Similarly, in copper-nickel alloy tubes, selective corrosion leads to the de-alloying of nickel. Uniform corrosion occurs when a uniform layer of rust forms on the surface of metals, spreading across the entire metal surface. This type of corrosion is commonly observed in metals that lack protective surface coatings. Metals such as aluminium, zinc, and lead are frequently affected by uniform corrosion.
Similar to other natural hazards, corrosion can lead to costly and hazardous damage in various things such as vehicles, water systems, pipelines, bridges, railway mast structures, and public buildings.
Here we discuss the effects of corrosion on railway mast structures:
-
Structural Weakness: Corrosion affects the ductility and tensile strength of the material, gradually weakening the metal components of the mast structure. Ductility refers to a material's ability to bend and stretch under stress without breaking. This characteristic is vital because it enables metal structures to endure loads that would otherwise cause them to fail. However, corrosion can diminish the ductility of a material by weakening its bonds and making it more fragile. This can result in the formation of cracks and eventual failure, particularly in areas exposed to high levels of stress. Tensile strength, on the other hand, measures a material's capacity to resist breaking when subjected to tension. It specifically represents the strength of the attractive forces between the lattice and atoms that counteract external forces. This property is crucial for maintaining the safety and reliability of structures. When corrosion affects tensile strength, the structural integrity becomes compromised.
-
Increased Maintenance Costs: Corroded mast structures require more frequent inspections, maintenance, and repairs, which can significantly increase maintenance costs for the railway system. In addition to costs related to maintenance and monitoring, there are potential expenses associated with production time, property damage, injuries, environmental impact, and reputation damage.
-
Electrical Disruption: Corrosion on the mast structure can affect the electrical conductivity and grounding of the overhead catenary system. This can result in disruptions to the power supply for trains, leading to service disruptions and delays. Also, electrical disruptions pose safety risks, as they can affect the proper functioning of signalling systems and communication networks, potentially compromising train operations and overall railway safety. Therefore, proactive corrosion prevention and maintenance measures are crucial to ensure reliable and uninterrupted power supply for smooth railway operations.
-
Aesthetic Impact: Corroded mast structures can have a negative visual impact, affecting the overall aesthetics of the railway infrastructure. This can have implications for the perception and image of the railway system.
Looking for a reliable manufacturer of railway electrification structures?
Explore Utkarsh Railway Electrification Structures. We have two state-of-the-art manufacturing facilities in West Bengal, spread over 100 acres with ample covered shed area. With our in-house hot-dip galvanising facilities and stringent quality control measures, we ensure high-standard coatings and finishes. We offer fabricated and galvanised steel structures for OHE (Overhead Equipment) and TSS (Traction Sub-Station), which are approved by RDSO/CORE and have a Core Item ID of 4200001. Our production capacity for railway electrification structures is impressive, exceeding 4000 MT per month, including portals and special span structures. We source steel from reputable manufacturers near our plants, enabling faster material procurement. Our strict quality assurance team checks every piece to ensure error-free products, and our efficient logistics department facilitates cost-effective transportation across the country. We maintain sufficient stock to book raw materials and complete inspections within 20-25 days through RITES, enabling us to provide immediate delivery to our clients.