Cable management and wire protection for high mast lighting systems
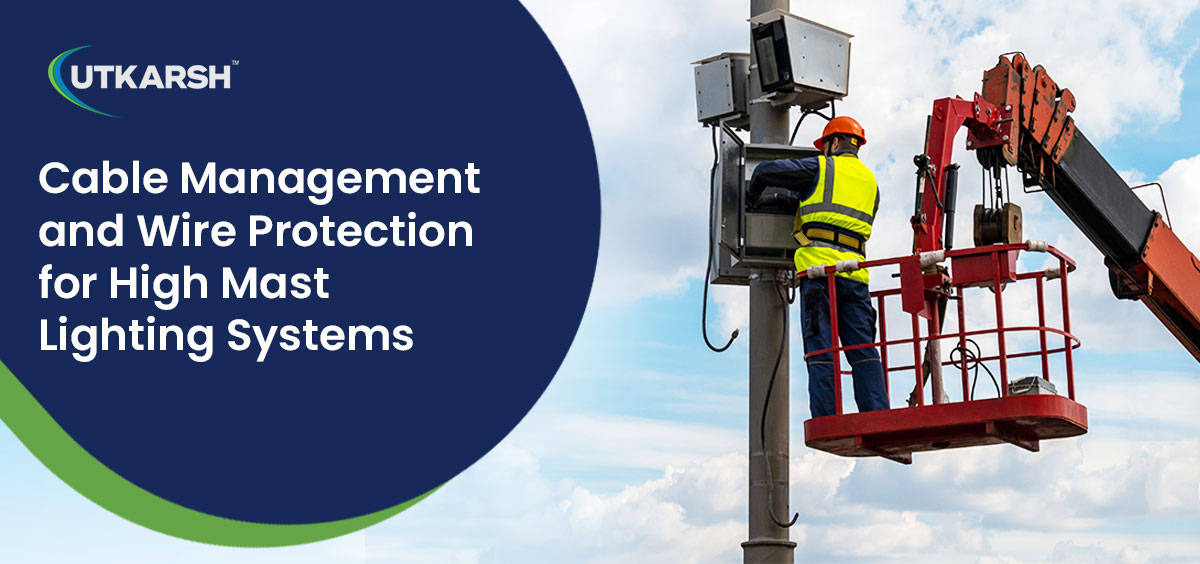
High mast lighting systems are essential for illuminating large outdoor spaces such as highways, airports, stadiums, and industrial areas. These systems consist of tall poles with multiple light fixtures mounted at significant heights, requiring efficient cable management and wire protection to ensure safe and reliable operation. Here, we share some of the insights into efficient cable management during and after high mast pole installation.
1. Cable routing and organisation.
- Cable trays: Install cable trays along the length of the mast to support and route cables. Cable trays ensure proper separation and organisation of cables, making it easier to identify and address any issues that may arise.
- Cable ties and clips: Secure cables to the mast structure using cable ties or clips at regular intervals to prevent them from hanging loosely and potentially getting entangled with moving parts or machinery.
- Segregation of power and control cables: Separate power cables from control or communication cables to minimise interference and ensure proper functioning of the lighting system.
2. Cable protection and insulation
- Conduit systems: Use conduit systems to enclose and protect cables from physical damage, UV exposure, and moisture.
- Cable glands and fittings: Install cable glands and fittings at entry and exit points of the mast to provide a secure and weatherproof seal. These components help prevent moisture ingress and protect the cables from external elements.
- Heat shrink tubing: Apply heat shrink tubing to individual cables or cable bundles to provide insulation and protection against abrasion, chemicals, and environmental factors. Heat shrink tubing shrinks when heated, creating a tight seal around the cable, ensuring long-term durability and reliability.
3. Bonding and grounding
- Grounding: It is important to ensure effective grounding of the high mast lighting system. This involves securely installing grounding rods or plates at the base of the mast and connecting them to the system's grounding conductor. Grounding helps to dissipate electrical charges and provides a safe path for current flow, reducing the risk of electrical hazards.
- Bonding: All metallic components of the system, including poles, fixtures, and cable trays, should be bonded to prevent differences in potential and mitigate the risk of electrical shock. Bonding conductors establish a continuous electrical connection between the various components, ensuring that they are at the same electrical potential.
4. Surge protection
Looking for a reputed high mast manufacturer in India?
Explore High Mast Lighting Systems from Utkarsh India. Our in-house design facilities include structural and foundation design capabilities, validated by IIT-Kharagpur using PLS and specialised software. Our high mast lighting systems are available in both three-point and two-point suspension configurations. To ensure durability, our systems feature rust-free electroplated rope drums, sprockets, and torque limiters. The rope drum is designed with left and right-hand grooves for better alignment of the ring, ensuring optimal performance. Lantern Rings are available in both detachable arm and fixed arm options.
To enhance corrosion resistance, we use a seven-tank galvanising process for better adhesion and uniformity. Our plants are equipped with comprehensive testing facilities, including a spectrometer for chemical analysis. All trailing cables comply with IS 9968 (P-1) standards for safety and durability. Stainless steel hardware is used to ensure a longer lifespan. The head frame is equipped with a stainless steel axle and an anti-rotation clamp to protect the axle from damage.
We also provide a stainless steel guide roller for smooth cable and rope movement. The lifting mechanism features a heavy-duty drive chain, and safety locking ropes are included for high mast safety. The motor is equipped with dual safety protection, both mechanical and electrical. Optional anti-theft nuts for foundation bolts, along with a specially developed wrench, are available. Prior to dispatch, all winches and motors undergo proper load testing. Structural designs are checked for all orders before production, ensuring quality and reliability. Wind tunnel testing is conducted at IIT-Kanpur to validate our designs for optimal performance in windy conditions.